Expert Container Welding Inspection Solutions for Quality Control and Conformity
Professional container welding evaluation solutions stand as the keystone of high quality control and conformity procedures adopted by sectors. From precise inspections to innovative techniques, the world of tank welding examination uses a sophisticated landscape of methods aimed at maintaining criteria and mitigating dangers.
Relevance of Storage Tank Welding Inspection
Making sure the quality of storage tank welding through precise examination is important in keeping structural honesty and preventing potential hazards in commercial setups. Tank welding plays an essential role in different sectors, including oil and gas, production, and chemical handling. The architectural integrity of storage tanks is vital to stop leaks, spills, and various other unsafe incidents that can result in environmental damages, economic losses, and also endanger lives.
Through extensive assessment procedures, welding issues such as cracks, incomplete fusion, and porosity can be determined and remedied without delay. Examinations also help guarantee compliance with market requirements and guidelines, giving a degree of guarantee pertaining to the top quality and safety of the bonded tanks.
Normal examinations not just boost the total top quality of container welding yet additionally add to the long life and dependability of industrial devices. By discovering and attending to problems at an early stage, business can avoid costly repairs, downtime, and potential crashes, eventually securing their operations and reputation.
Advanced Inspection Strategies
One innovative method that has actually transformed container welding evaluation is the usage of automated ultrasonic testing (AUT) This technique eliminates human error and makes certain extensive insurance coverage of welds, improving the general top quality of evaluations.
In addition, phased range ultrasonic screening (PAUT) is another sophisticated examination technique getting appeal in tank welding evaluations. Tank Welding Inspection Service. PAUT enables precise control over the ultrasonic beam of light angle and centerpiece, making it possible for inspectors to find and characterize problems with high resolution. This method is specifically effective in examining complicated geometries and can supply thorough imaging of weld defects for complete evaluation
In enhancement to AUT and PAUT, advanced radiographic testing methods, such as digital radiography, are being significantly made use of in container welding inspections. These techniques provide improved picture high quality, minimized examination times, and boosted safety and security contrasted to traditional radiographic methods. By including these sophisticated assessment strategies, sectors can ensure better control and compliance with regulatory criteria in container welding procedures.
Trained Evaluation Professionals
Proficiency in inspection strategies is extremely important for making sure the accuracy and reliability of container welding assessments in industrial setups. Trained inspection specialists play a vital function in upholding top quality control requirements and ensuring conformity with regulatory needs. These experts undergo strenuous training to establish proficiency in numerous evaluation methods, including aesthetic testing, ultrasonic screening, radiographic testing, and magnetic fragment testing.
Qualified inspection specialists are well-versed in translating codes and standards specific to storage tank welding, such as API 653 and API 650. They have the understanding and skills to identify welding flaws, assess weld high quality, and make educated decisions relating to the reputation of welded joints. Furthermore, these specialists are trained to continue reading this operate innovative inspection devices and make use of specialized tools to carry out detailed evaluations of storage tank welds.
Cost-efficient Quality Assurance Solutions
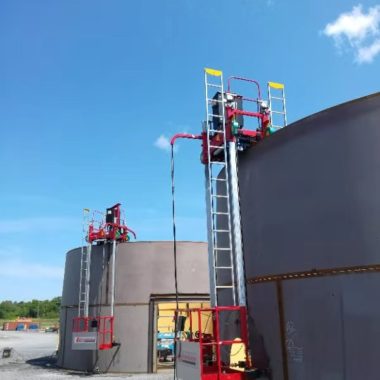
In the middle of the obstacles of maintaining high requirements in storage tank welding inspections, the quest for economical top quality control solutions emerges as a pivotal focus for commercial operations. Carrying out reliable quality control steps is important to ensure weld integrity, stop issues, and promote security requirements. One economical remedy is the application of innovative inspection technologies such as automated welding inspection systems. These systems can improve the evaluation process, decrease human error, and enhance overall productivity.
Along with technological developments, establishing a thorough high quality control plan that includes normal assessments, documentation, and employee training can dramatically contribute to cost financial savings in the long-term. By purchasing training programs for welding assessors and guaranteeing adherence see this here to industry requirements, business can proactively recognize problems, reduce rework, and stay clear of expensive repairs.
In addition, outsourcing customized assessment services when needed can be an economical strategy for firms that do not have the competence or sources in-house. Collaborating with reliable examination firms can supply access to proficient professionals and innovative equipment without the requirement for significant capital expense. Ultimately, prioritizing cost-effective high quality control services is important for attaining operational effectiveness, conference image source regulatory demands, and supplying premium bonded tanks.
Ensuring Regulatory Compliance
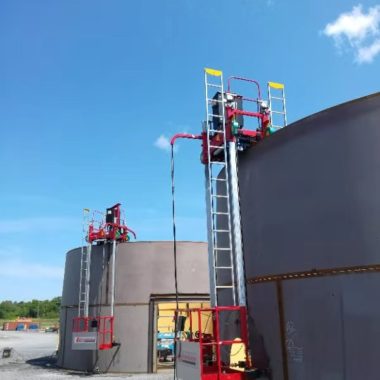

Regulatory compliance in storage tank welding examinations is a fundamental aspect of making sure sector criteria and safety and security requirements are met. Adhering to regulative guidelines set forth by companies such as the American Petroleum Institute (API) and Occupational Safety And Security and Wellness Management (OSHA) is critical to guaranteeing the integrity and reliability of welded tanks. These regulations outline particular criteria for welding procedures, material specifications, inspection methods, and quality control measures that must be complied with to keep functional excellence and avoid prospective risks.
To guarantee regulatory conformity in container welding assessments, qualified welding inspectors must have a thorough understanding of the relevant codes and requirements. Routine audits and assessments need to be performed to confirm that welding processes and treatments line up with regulative requirements. In addition, paperwork and record-keeping are vital components of conformity, supplying a transparent route of adherence to guidelines for auditing objectives.
Final Thought
Finally, specialist storage tank welding inspection remedies play a vital role in making certain the quality assurance and compliance of containers. By utilizing innovative evaluation methods and trained specialists, companies can properly keep an eye on the welding process, determine possible issues, and keep regulatory conformity (Tank Welding Inspection Service). This positive strategy not only assists in preventing pricey repair work and downtime yet also makes sure the safety and stability of the containers
From precise assessments to advanced methods, the world of tank welding evaluation supplies a sophisticated landscape of methods intended at promoting standards and mitigating dangers.In addition, phased array ultrasonic testing (PAUT) is one more innovative inspection technique getting appeal in container welding inspections.Proficiency in evaluation methods is extremely important for ensuring the accuracy and reliability of storage tank welding assessments in commercial setups. One cost-efficient remedy is the utilization of advanced inspection technologies such as automated welding evaluation systems.In final thought, expert tank welding evaluation services play a vital function in making sure the high quality control and compliance of storage tanks.